Making manufacturing intelligent with SAP MII
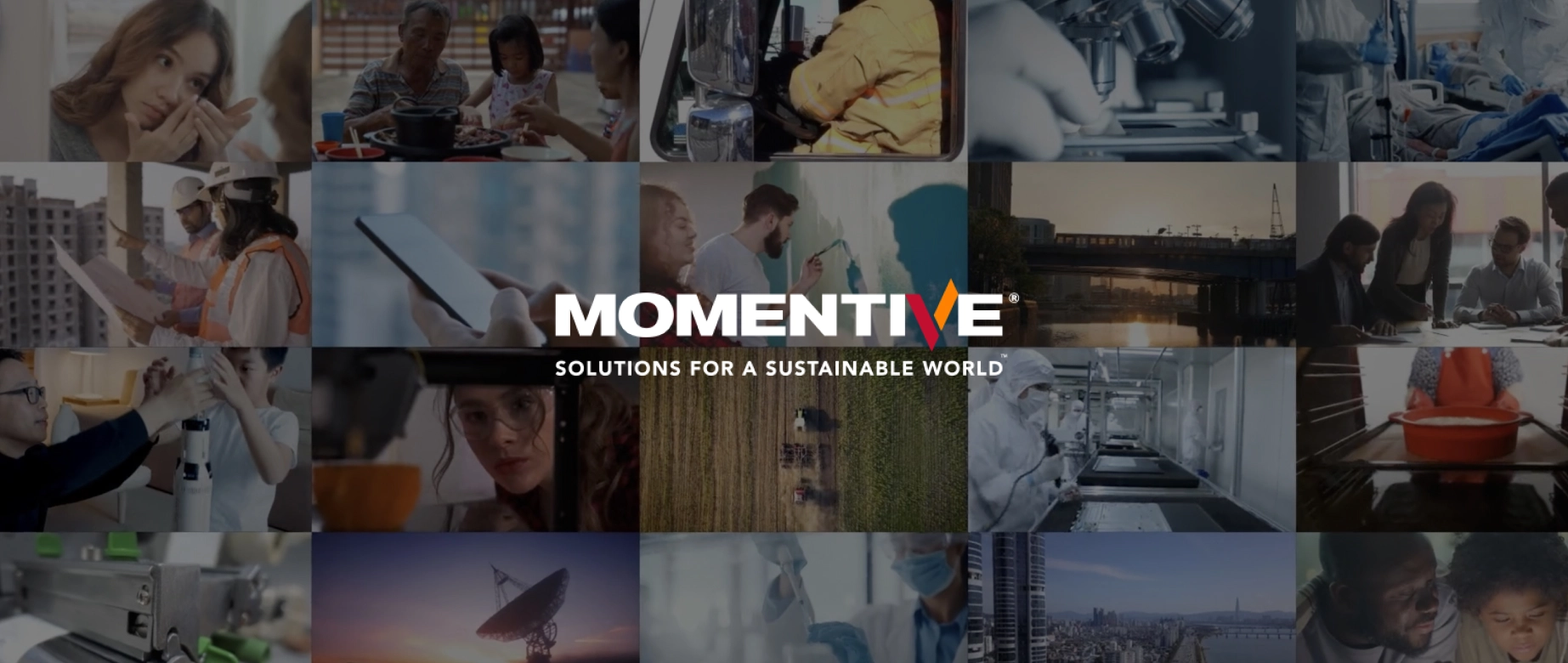
Key challenges
Disjointed processes and reliance on conventional operational methods had resulted in inefficient operational management.
There was a lack of interoperability between shop-floor systems, tools, and backend ERP systems increased shop-floor turnaround times and introduced inaccuracies in person-hour calculations.
Unstructured plant data and process inconsistencies negatively impacted overall productivity.
Non-collaborative practices among plants, business processes, and systems led to a fragmented operational environment, raising costs. Challenges in measuring and monitoring KPIs hindered the development of core competencies.
Client in spotlight
Based in New York, USA, our client stands as a worldwide frontrunner in silicones, resins, and advanced materials, boasting a rich legacy spanning over 80 years with an annual revenue of USD 6.5 Bn+. With a workforce exceeding 9000 employees, the client is dedicated to providing science-based solutions to a customer base of over 4000 customers from various industries, including real estate, electronics, automotive, oil and gas, consumer goods, and personal care in 100-plus countries.
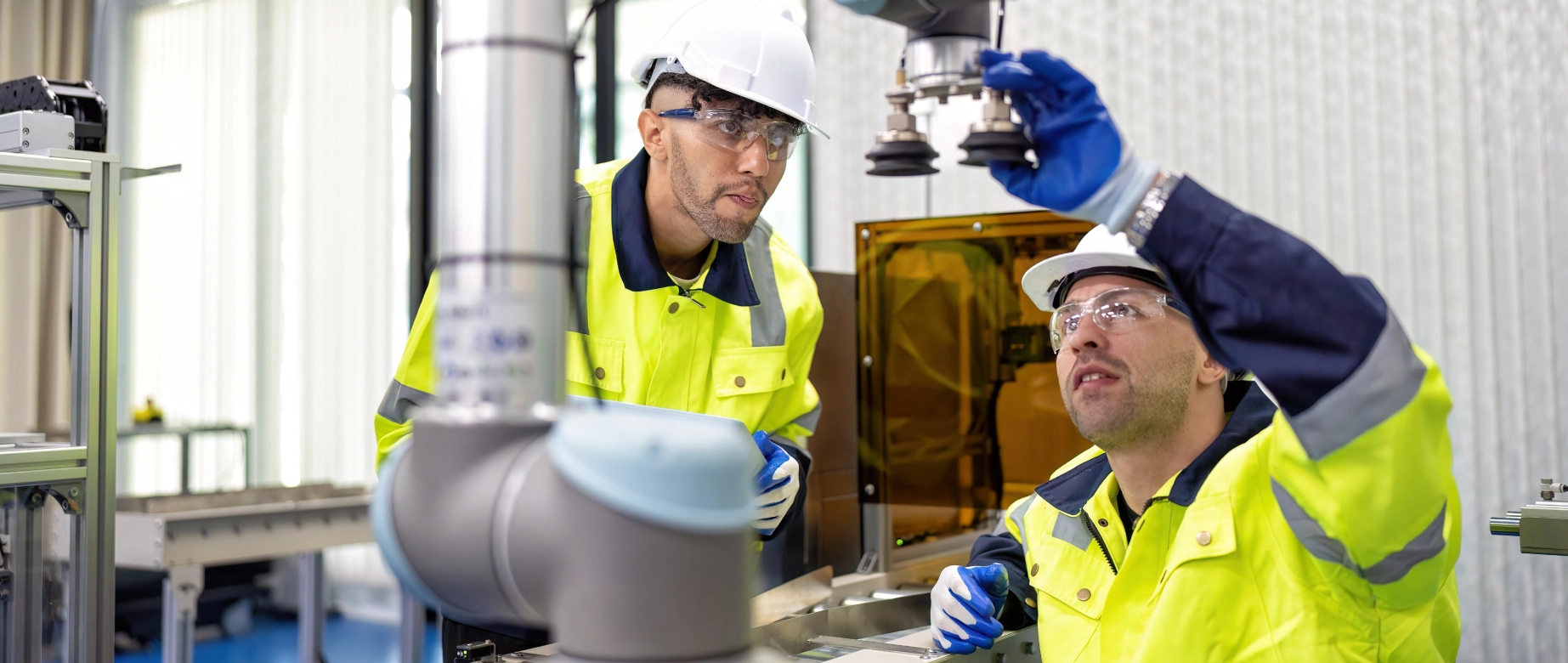
Unlocking Digital success



Project outcomes
Automated workflows and synchronized manufacturing operations
Up to 100% monitoring, tracking, and traceability of KPIs - in real-time
Elevated employee productivity and shortened sales cycle times
Optimized operations with real-time reporting capabilities, improved visibility, and enhanced competencies
Overall Equipment Effectiveness (OEE) enhanced by the shop floor tools and systems
Download Success Story
Dive deeper into the complete solution. Access the detailed success story in the PDF.